Für den Präzisionsfertiger „Harry Roth“ aus Waldkirch war das vergangene Jahr hart: als Zulieferer für die Flugzeugindustrie brach von heute auf morgen der wichtigste Geschäftszweig ein. Statt erhofften Aufschwungs hohe Umsatzeinbußen, dazu ein neuer Standort. Trotzdem wurden neue Chancen und Qualitäten genutzt.
VON ANNA-LENA GRÖNER
Noch etwas einsam steht der große Neubau der Firma „Harry Roth“ im sogenannten „Brunnenrain“ im Waldkircher Osten. Der moderne grauweiße Beton- und Stahlbau ist umgeben von Wiesen und Schrebergärten auf der einen und der B294 auf der anderen Seite. Vor genau einem Jahr wurde das rund sieben Millionen teure Gebäude bezogen, den Start hatte sich das Unternehmen anders vorgestellt.
Schon der Umzug mitten in der Pandemie war eine Herausforderung. Drei Wochen dauerte er, tonnenschwere Maschinen mussten verladen werden, die Produktion stand mehrere Tage still. Das kostete Nerven und bares Geld und das in einer Zeit, in der die Geschäfte ohnehin bescheiden laufen: Als Präzisionsfertiger von Dreh-, Fräs- und Schleifteilen beliefert „Harry Roth“ vor allem die Luftfahrt. Seine Produkte gehen unter anderem an den weltgrößten Flugzeughersteller Airbus oder auch an den brasilianischen Flugzeugbauer Embraer.
Airbus hatte im vergangenen Jahr 34 Prozent weniger Flugzeuge ausgeliefert, weltweit hoben 43 Prozent weniger Flieger ab. Eine regelrechte Bruchlandung für das Geschäftsjahr von „Harry Roth“. „Die Aufträge aus der Luftfahrt gingen um knapp 40 Prozent zurück“, sagt Geschäftsführer Robert Bischoff und lehnt sich mit besorgter Mine in seinem Stuhl zurück. In normalen Jahren erwirtschaftet der Metall-Verarbeiter gut sieben Millionen Euro, das vergangene Jahr bescherte einen Umsatzrückgang von 30 Prozent.
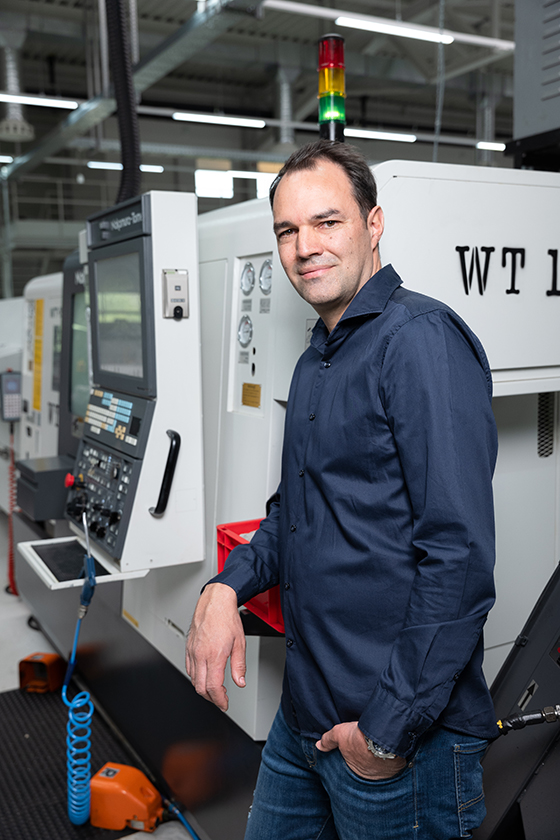
Die große Fensterfront aus Bischoffs Büro eröffnet den Blick auf die Kreisstadt mit der Kastelburg am Hang sowie auf die gegenüberliegende grüne Wiese. Erst 2025 sollen Nachbarn kommen, der Waldkircher Verpackungsspezialist „Faller Packaging“ plant dort seinen 50-Millionen Euro Neubau. Auch der Nachbarschreibtisch in Bischoffs Büro ist an diesem Tag unbesetzt, nur noch selten sitzt hier Vater Manfred, er genieße seinen wohl verdienten Ruhestand beim Jagen und Schnapsbrennen.
Die Familie stammt aus der Nähe von Rottweil, dort lebt Robert Bischoff noch immer, pendelt fast täglich nach Waldkirch. „Mein Vater, mein Bruder und ich haben 2006 die Firma übernommen“, sagt Robert Bischoff. Gegründet wurde das Unternehmen 1937 vom Namensgeber Harry Roth, der es in den 80er Jahren an eine Firmengruppe verkaufte, die wiederum 1998 Konkurs ging. Inzwischen leitet Robert Bischoff das Unternehmen, sein Bruder Lars hält die Stellung in der zweiten Firma der Familie, „Kaiser Metallwaren“ in Mönchweiler bei Villingen-Schwenningen.
Alles unter einem Dach
Der studierte Maschinenbauer Robert Bischoff zeigt durch die Fensterfront seines Büros auf zwei Krane, die zwischen Häuserdächern, nur wenige hundert Meter Luftlinie entfernt, hervorlugen. Im „Papiergässle“ lag der alte Firmensitz. Insgesamt vier Gebäude hatte das historische Wachstum hervorgebracht, effizientes Arbeiten und weiterer Ausbau waren an diesem Standort unmöglich.
Jetzt entstehen dort zehn Mehrfamilienhäuser. Am neuen „Harry Roth“ Geschäftssitz arbeiten alle 50 Mitarbeiter unter einem Dach. Verlässt Bischoff sein Büro in der dritten Etage, so hat er über schalldichte Fenster im Flur einen beeindruckenden Blick in die 40 mal 70 Meter große Produktionshalle. An den mächtigen, teilweise 700.000 Euro wertvollen Maschinen wird fleißig gearbeitet. Es gibt also etwas zu tun.
Durch die Pandemie habe man sich produkttechnisch etwas breiter aufgestellt, „wir machen inzwischen zum Beispiel auch Teile für E-Bikes, was wirklich gut funktioniert“, sagt der 40-Jährige. Sobald Bischoff die Tür in die Halle öffnet, schallt ihm das Schnaufen, Brummen und Klacken der rund 30 CNC-Maschinen entgegen.
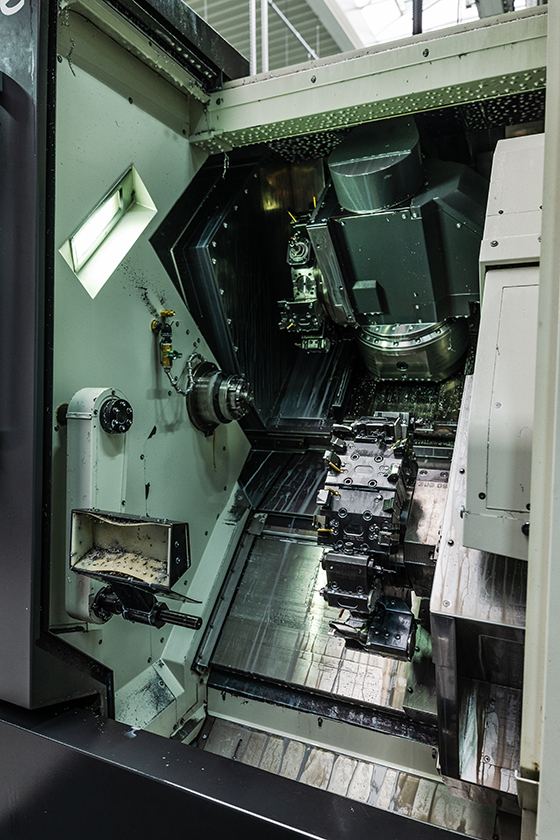
Hier schlägt hörbar das Herz des neuen Firmengebäudes. Bedient werden die Maschinen vor allem von Männern in blauen Arbeitshosen, alles gelernte Zerspanungsmechaniker. Sie geben die richtigen Steuerinformationen ein, führen das Rohmaterial zu (zum Beispiel Stahl und Edelstahl, Aluminium, Titan, Messing oder auch Kunststoffe) und machen stichprobenartig Kontrollen, dazu stehen neben jeder Maschine auf einem Arbeitstisch jeweils eine große Lupe und ein Mikroskop.
An zwei Tischen im hinteren Bereich der Halle sitzen Mitarbeiterinnen, blicken durch große beleuchtete Lupen und entdrahten mit entsprechendem Kleinstgerät die gefertigten Metallteile. Ausgespuckt wurden die zuvor von den gigantischen Drehfräsen: so werden lange Metallstangen beispielsweise zu filigranen Drehteilen, die in Flugzeuglandeklappen eingesetzt werden.
Sichtbar als attraktiver Arbeitgeber
An einer anderen Drehfräsmaschine werden schwere, etwa sieben Zentimeter dicke und 15 Zentimeter breite Metallkreise zu schmalen runden Bauteilen, die später in der Klimasteuerung von Flugzeugen zum Einsatz kommen. Blick nach vorn Der neue Firmensitz ermögliche effizienteres Arbeiten in vielen Bereichen, so Bischoff. Er zeigt alle Stationen der Produktion, erklärt, was wo gemacht wird, nimmt immer wieder gefertigte Teile in die Hand und beschreibt, wo sie zum Einsatz kommen: Buchsen für Flugzeugfahrwerke, Adapter für Beatmungsgeräte oder Kunststoffteile für OP-Tische.
Die Kunden kommen aus der Elektro- und Antriebstechnik, der Pneumatik und Hydraulik, dem Maschinenbau oder der Medizintechnik. Robert Bischoff führt stolz durch das neue Geschäftsgebäude: vom Keller, wo sich Pelletheizung, moderne Lüftungsanlagen und eine Wärmerückgewinnung für die Produktion befinden, über die Versandstation, wo die fertigen Waren von Speditionen und Paketdiensten abgeholt werden und ein platzsparendes Hochregal für bessere Übersicht und Lagerung sorgt, bis hin zum Vertrieb im zweiten Stock, der Qualitätskontrolle und dem Aufenthaltsraum mit großer Außenterrasse, wo gerade ein paar Mitarbeiter ihre Pause in der Sonne genießen.
Am Ende des Rundgangs sitzt Robert Bischoff wieder in seinem Stuhl im Büro im dritten Stock, blickt aus dem Fenster und sagt: „Mit dem neuen Bau wollen wir uns auch nach außen als attraktiver Arbeitgeber präsentieren, wir wollen, dass unsere Mitarbeiter gerne hier arbeiten.“ Ab September kommen drei neue Auszubildende in den Betrieb, eine neue Generation Zerspanungsmechaniker. Das vergangene Jahr ist passiert, die nächsten werden besser, da ist sich der Geschäftsmann sicher. Noch in diesem Jahr rechnet Bischoff mit einer deutlichen Erholung und plant daher, kräftig in neue Maschinen zu investieren.