Die textile Unternehmenswelt in Südbaden hat einige Hidden Champions zu bieten, deren Produkte für die Industrie in verschiedenen Ausführungen beim Endkunden ankommen. Drei Beispiele.
VON DANIEL RUDA
Das Logo überm Herzen
Die Wahrscheinlichkeit, dass Leser und Leserinnen von netzwerk südbaden T-Shirts, Pullover oder Hemden in ihren Schränken liegen und hängen haben, an deren Produktion das mittelständische Freiburger Unternehmen Madeira einen kleinen Anteil hatte, ist groß. Sehr groß sogar. Madeira stellt Stickgarn her und ist laut eigener Aussage Weltmarktführer auf diesem Gebiet. Bei so gut wie jedem bekannten Label, sei es Haute Couture, Mainstream oder Sportmode, kommen Garne aus Südbaden zur Verzierung zum Einsatz. In den meisten Fällen werden damit Logos oder andere Designs auf ein Kleidungsstück genäht. Stickgarn ist quasi das repräsentative Garn, das Nähgarn wiederum hält die Kleidung zusammen.
Markennamen darf er offiziell aber nicht nennen, erklärt Sebastian Schade, Marketing- und Vertriebsleiter. Wegen Vertragsinhalten und Diskretion. Madeira, ein familiengeführtes Unternehmen, das 2019 sein 100-Jähriges feierte, ist ohnehin eine zurückhaltende Adresse, wenn es um Öffentlichkeit geht. Wirtschaftliche Zahlen werden nicht verraten und das Inhaber-Brüderpaar Ulrich und Michael Schmidt aus der dritten Generation der Madeira Garnfabrik Rudolf Schmidt KG überlässt Marketingleiter Schade das Sprechen über das, was hier – und an neun Niederlassungen weltweit – geschieht.
Es ist eine Menge, und Schade kann alles abspulen. Rund zwölf Millionen Spulen an Garnen – die meisten mit jeweils 5000 oder 1000 Metern – stellt Madeira pro Jahr her. 80 Prozent davon in Freiburg, den Rest an Produktionsstätten in China und Indonesien, wo für den asiatischen Markt produziert wird. Die Produktpalette beinhaltet unter anderem Garne aus Viskose, Polyester oder Wolle. Die Exportquote in Freiburg liege bei 90 Prozent, in über 100 Länder werde verschickt, vor allem in die USA, den größten Markt, sagt Schade im Besprechungsraum, dessen Decke so hoch ist, als sitze man in einer Kirche. Links und rechts ist man von riesigen Wandgemälden umgeben.
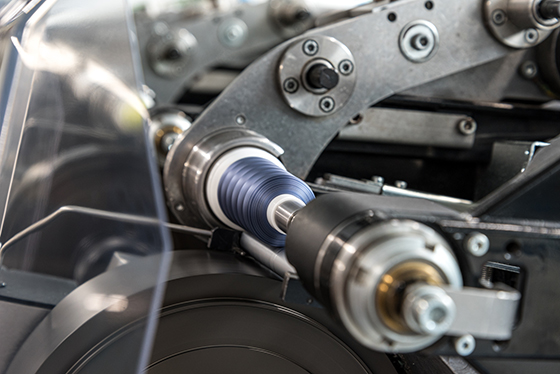
400 Mitarbeitende hat Madeira, die Hälfte davon in Freiburg. Die Firma sei die letzte ihrer Art, die in Deutschland noch Stickgarn herstelle. Der Rest komme aus Asien, erzählt Schade.
Ein paar Treppenstufen weiter unten befindet sich die Produktion, die mit den Jahren immer mehr gewachsen ist und trotz aller technischen Moderne damit leben muss, dass der ein oder andere Weg etwas länger ist, als er in einem Neubau wohl wäre. Die Maschinen rattern, in einem Raum zieht eine die weißen unbehandelten Garne, die als Rohmaterial in der Firma ankommen, von einer großen auf viele kleinere Spulen. Anschließend geht es in die hauseigene Färberei samt eigenem Labor am zweiten Freiburger Standort ein paar Kilometer entfernt, wo die Garne in einem komplexen maschinellen Verfahren bunt eingefärbt werden. „Nimmt man alles zusammen, haben wir fast 1000 Farbrezepte“, sagt Schade, der über die Zusammensetzung, die Haptik und eben die Farbe der Garne ausführlich referieren kann.
Es sind gute Zeiten, die Madeira erlebt. Aus der Coronakrise kam das Unternehmen überraschend gut heraus. Schade berichtet von 30 Prozent Wachstum gegenüber der Prä-Coronazeit, was Produktionsmenge und Umsatz angeht. Die Zuverlässigkeit und der über die Jahrzehnte erreichte Produktionsstandard haben daran großen Anteil. „Wir sind ein kerngesundes Unternehmen“, betont Sebastian Schade.
Das Produkt, das keiner sehen will
Etwas weniger als 100 Kilometer weiter südlich sitzt am Hochrhein in Bad Säckingen das Unternehmen Global Safety Textiles (GST). Dessen markiger Name hat Wahrheitsgehalt, wenn man ihn auf die Automobilindustrie und das Stück Stoff bezieht, das hier gewebt wird. „Wir produzieren den Luftsack für die Airbags im Auto“, erklärt Geschäftsführer Uwe Zimmermann. Das Geschäft im Autoland Deutschland läuft, 200 Mitarbeitende beschäftigt GST am Hochrhein, neben Bad Säckingen gibt es auch ein paar Kilometer weiter in Murg ein Werk.
Zurückhaltung in Sachen Markennamen gibt es bei Zimmermann nicht: „Wir machen Airbags für den VW Polo genauso wie für einen Ferrari oder Lamborghini“. Die Qualität der Ware muss für jeden Auftrag gleich hoch sein. Qualitätsabfall dürfe nicht sein, das gebe er seinen Angestellten regelmäßig mit auf den Weg. „Wir stellen etwas enorm Wichtiges her, was hoffentlich nie zum Einsatz kommen muss“, sagt der 61-Jährige.
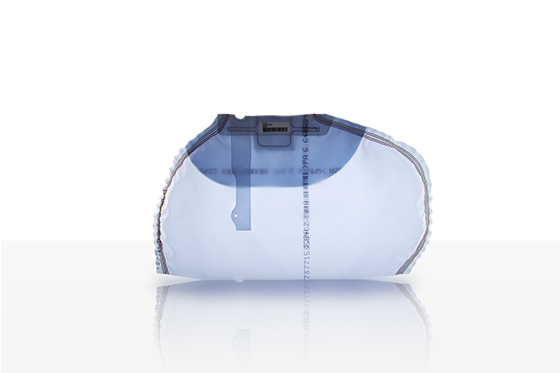
Die technischen Textilien haben am Hochrhein Tradition, schon Mitte des 19. Jahrhunderts sei hier gewebt worden. Früher trieben Wasserkraftwerke die Webmaschinen an. Als in den 1980er Jahren und vor allem den Neunzigern der Airbag zum Standard wurde und in Nylonform gewebt wurde, spezialisierte man sich am Hochrhein darauf.
Angekommen im Heute ist Global Safety Textiles – in der Vergangenheit hatte die Firma schon ein paar andere Namen – unter dem Dach des koreanischen Hyosong Konzerns. Der Hochrhein ist der einzige Standort in Deutschland innerhalb der GST-Gruppe neben Südafrika, China, Rumänien und Mexiko. Sogenannte One-Piece-Woven, also einzeln gewebte Stücke, werden hier vor allem in einer speziellen Verfahrenstechnik großer Maschinen gefertigt. So muss anschließend nicht mehr genäht werden, wie es sonst der Fall ist, und es sollen Autoinsassen durch spezielle Ausdehnungen der Luftsackkammern bei einem Aufprall von Kopf, Schulter oder Brustkorb geschützt werden.
Es ist eine komplexe Sache, und das Geschäft läuft. Bis zu fünf Millionen Airbags pro Jahr kann das Werk herstellen – darin ist auch jener im Vergleich kleine Bereich eingerechnet, in dem Stoffrollen von mehreren Hunderten Metern pro Auftrag das Werk verlassen, damit anderswo die Airbag-Form herausgeschnitten und vernäht wird.
Wegen der sich in Zukunft verändernden Mobilität, in der es weniger Autos geben soll, macht sich Uwe Zimmermann keine allzu großen Sorgen ums Geschäft, auch wenn der Markt umkämpft sei, Preisdruck herrsche und die Produktion in anderen Ländern kostengünstiger als in Deutschland sei: „Ich denke, dass es zum Beispiel durch das autonome Fahren noch mehr Airbags brauchen wird.“ Schließlich könne ja in Zukunft nicht davon ausgegangen werden, dass die Passagiere noch so im Auto sitzen, wo und wie sie es bisher tun. „Wahrscheinlich braucht es einmal Airbags, die aus allen möglichen Richtungen im Inneren eines Autos kommen, nicht mehr nur durch das Lenkrad“. Dennoch will sich das Unternehmen diversifizieren und nicht mehr alleine vom Airbag abhängig sein. Im Outdoorbereich gebe es etwa Nischen, in die GST stoßen will, zum Beispiel bei der Herstellung von Markisenstoffen. Es wäre ein Stoff, den man auch im Einsatz sehen möchte.
Zum Bedienen des Teebeutels
Schon der Name hat etwas Heimeliges. Zwirnerei an der Wutach heißt das Familienunternehmen mit 40 Mitarbeitenden, das im kleinen Stühlingen am Rand des Landkreises Waldshut auf der grünen Wiese und direkt an einem Seitenarm des Flusses Wutach steht. Ein paar Meter weiter, auf der anderen Flussseite, ist die Schweiz. 1886 ist die Firma gegründet worden. „Historisch angefangen hat es hier an diesem Standort mit Baumwollzwirnen, später kamen dann auch Garne und Zwirne aus synthetischen Fasern hinzu, die zum Beispiel in der Fischerei ihre Verwendung fanden“, erzählt Patrick Steinweg, der das Unternehmen gemeinsam mit seinem Bruder Marcel leitet und die fünfte Generation darstellt.
„Wir verzwirnen hier Garn“, sagt der 41-Jährige und erklärt, was das bedeutet: „Einfach gesagt wird dabei Garn, oder im Volksmund Fäden, nebeneinandergelegt und danach zusammengedreht. Das nennt man Verzwirnen“. Was dabei herauskommt, ist ein stabiles, gleichmäßiges Produkt, das reißfest sein und unterschiedlichen Hygiene- und Sicherheitsstandards genügen muss.
Das verzwirnte Garn, das je nach Dicke mit bis zu 20.000 Metern Länge auf Spulen gewickelt wird, die zwischen 200 Gramm und 7,5 Kilogramm schwer sein können, endet in der Lebensmittel- und Hygienebranche sowie in der Verpackungsindustrie. Vor allem an Teebeuteln, Tampons und aufreißbaren Verpackungen etwa von Mehl oder Kaffee. In wohl jedem Teeregal in einem Supermarkt, ob im In- oder Ausland, finden sich die Stühlinger Garne, erzählt Patrick Steinweg.
Das kleine Unternehmen hat weltweit Kunden, der Exportanteil liege bei mehr als 75 Prozent. Kunden in mehr als 70 Ländern sind die Adressaten. Europa und daneben die USA sowie der asiatische Raum die Hauptmärke. „Wir sind in einer Nische, in der wir uns durch unsere Qualität über die vielen Jahre einen guten Ruf erarbeitet haben“, sagt Patrick Steinweg. Selbstverständlich ist das nicht, vergangenes Jahr hat die andere traditionelle Zwirnerei in Untereggingen, keine zehn Kilometer entfernt, wegen wirtschaftlicher Probleme schließen müssen. So etwas soll in Stühlingen nicht passieren, wo der Umsatz stabil bei 12 Millionen pro Jahr liegt: „Wir müssen weiter auf unsere langjährigen Partnerschaften mit Kunden setzen und Qualität liefern.“