Mehr als sauber: Im Reinraum muss die Luft wirklich nahezu komplett rein sein. Wie das geht und wie die Arbeit im Inneren aussieht, haben wir uns vor Ort angeschaut: bei TDK-Micronas. Das Unternehmen entwickelt, produziert und testet seine Sensoren in Freiburg und verschickt sie von hier in die ganze Welt.
Text: Julia Donáth-Kneer
Schutzanzug, Überzieher für Kopf und Schuhe – dabei gehen wir nicht mal in den echten Reinraum, sondern nur in den Besuchergang, der außen am rund 3600 Quadratmeter großen Reinraum der TDK-Micronas vorbeiführt. Mit dabei: Dirk Heinen. Der promovierte Physiker ist Leiter Frontend-Fertigung der sogenannten Waferfab beim Freiburger Sensorenhersteller, der seit 2016 Tochter des japanischen Elektronikriesen TDK ist.
Rund 1000 Mitarbeitende arbeiten in Freiburg, im Vergleich zu anderen großen Chip- und Sensorenherstellern eher ein kleines Unternehmen. Doch das hat Vorteile. Denn viele Waferfabs entwickeln Microchips zum Beispiel in Amerika, produzieren in Fernost, testen und bauen in Südostasien auf. Im Unterschied zu Micronas-TDK: „Wir entwickeln, produzieren und testen einzelne Produkte noch komplett am eigenen Standort, was sehr ungewöhnlich für ein Halbleiterunternehmen ist“, sagt Dirk Heinen, der seit 28 Jahren im Unternehmen ist.
Der Fertigungsprozess eines Microchips spielt sich im mikroskopischen Bereich von Tausendsteln und Zehntausendsteln Millimetern ab. Ausgangsmaterial sind dünne Scheiben aus hochreinem Silizium, sogenannte Wafer. In einem nahezu partikelfreien Reinraum in der Waferfab entstehen in einer komplexen Abfolge chemischer und physikalischer Prozesse mehrere tausend integrierte Schaltungen pro Wafer, die später als Microchips verkauft werden können.
Hier, im Freiburger Industriegebiet Nord, entstand über die Jahre eine circa 3600 Quadratmeter große Reinraumfläche in zwei Gebäuden, verbunden über eine Reinraumbrücke. Wer einmal drin ist, kann sich im Inneren von Raum zu Raum bewegen, ohne erneut die Schleusen passieren zu müssen. Die Vorgaben sind streng. Das erlaubte Partikelniveau von Reinräumen wird in verschiedene Klassen eingeteilt. Reinraumklasse 1, nach der auch dieser hier klassifiziert ist, ist dabei die reinste, das heißt, die maximal erlaubte Partikelkonzentration ist am geringsten. Die Mitarbeitenden sind deutlich mehr eingepackt als wir im Besuchergang: Gamaschen bis zu den Knien, kompletter Schutzanzug mit Haube, Mundschutz und Handschuhe. Auf ihrem Rücken stehen die Namen, sie wären sonst nicht zu erkennen.
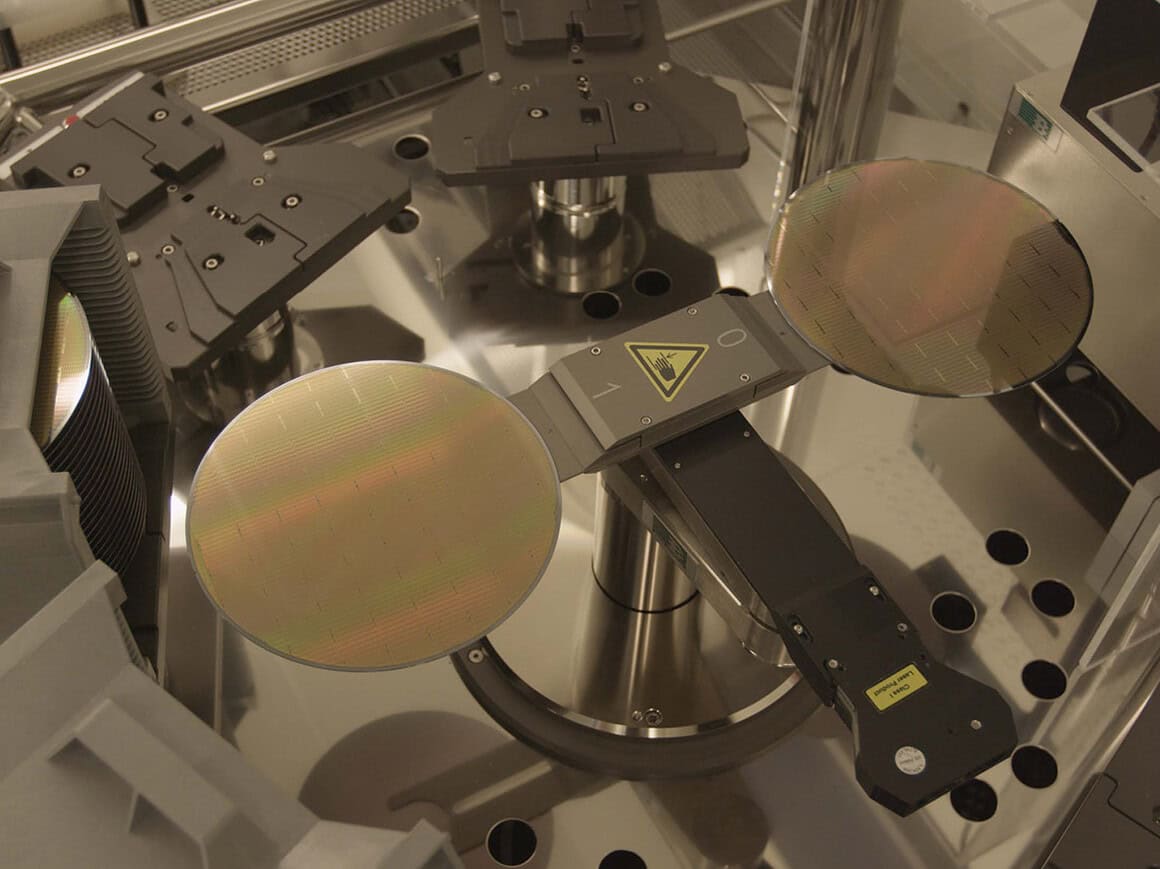
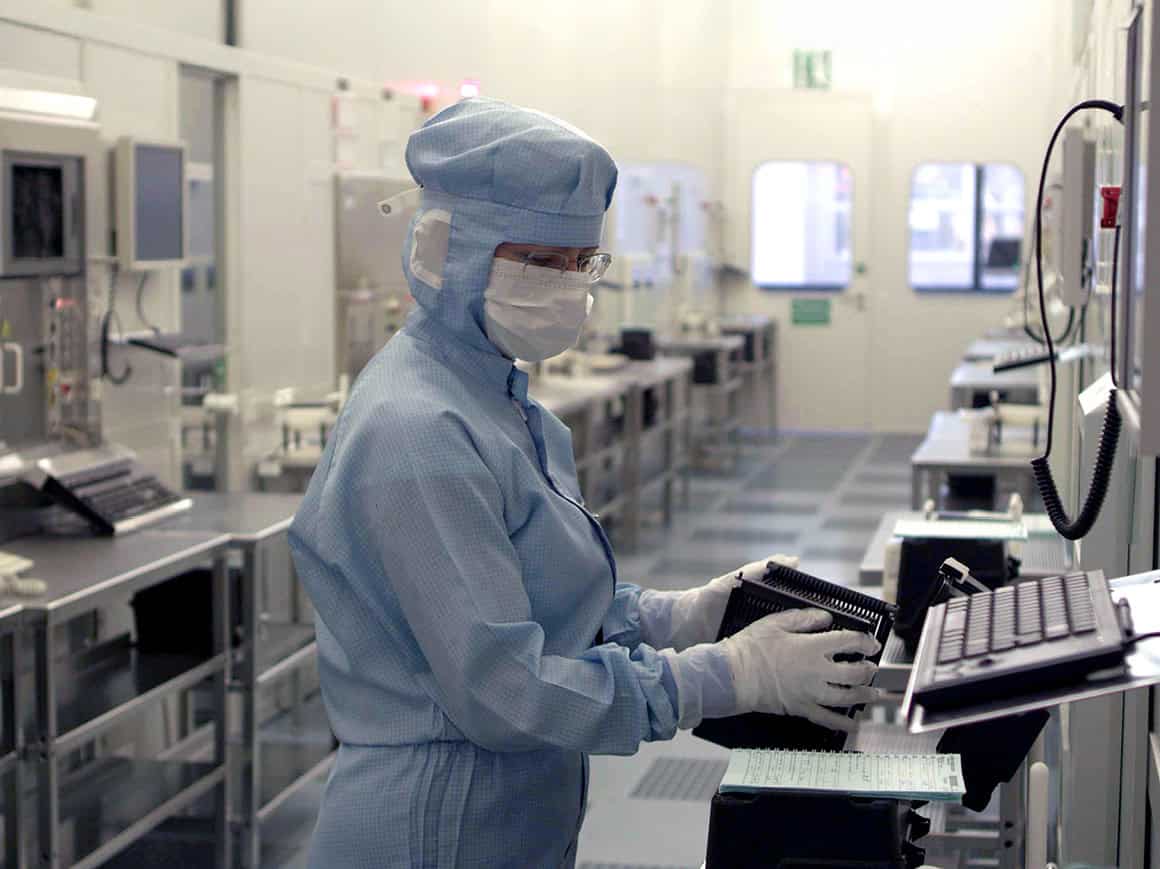
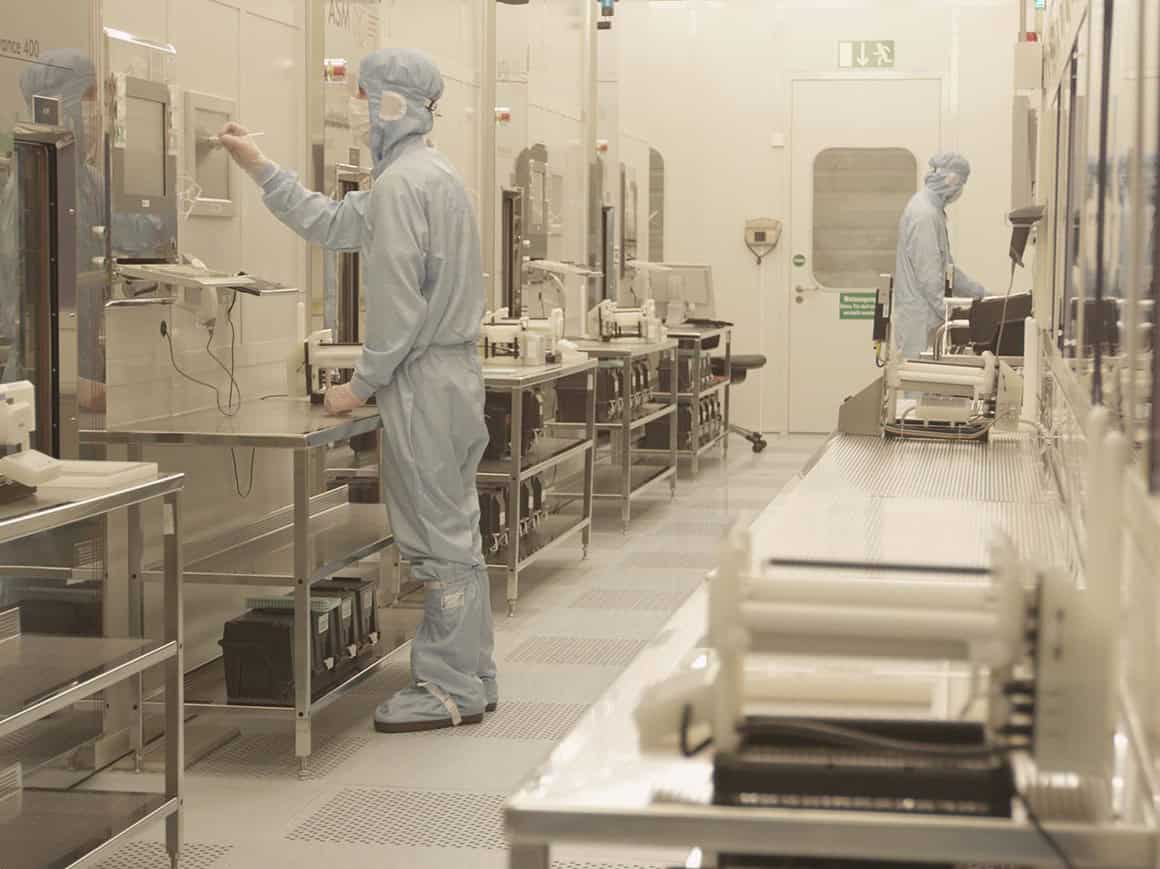
Dass Reinräume in verschiedenen Bauabschnitten realisiert werden, kennt Timo Porta gut. Der Maschinenbauingenieur ist einer von drei Geschäftsführern der CRC Clean Room Consulting GmbH. Das 1983 gegründete Unternehmen berät und plant Reinräume vor allem in der DACH-Region. Aktuelles Projekt: ein 4000 Quadratmeter großer Reinraum, für den mehr als 500 Bohrpfähle nötig sind, die jeweils einen Meter dick und 20 Meter tief im Boden verankert sind, um Schwingungseinflüsse von außen zu eliminieren. Kostenpunkt für einen Quadratmeter: rund 40.000 Euro, Bauzeit: vier Jahre. Kunden von CRC sind zum Beispiel Bosch oder Infineon, die genau wie TDK-Micronas in der Halbleitertechnik zu Hause sind, aber auch Pharmaunternehmen. Die Ansprüche an die Reinraumklassen unterscheiden sich je nach Branche, erklärt Tim Porta: „Während in der Pharma die Sterilität der Umgebung die entscheidende Größe ist, geht es bei Mikroelektronik um Partikelfreiheit.“ Auch die baulichen Herausforderungen sind andere: „Schwingungen sind bei den Pharmafirmen eher zweitrangig, da darf sogar ein Lkw vorbeifahren. In der Halbleitertechnik können jegliche Einflüsse von außen entscheidend sein.“ Bei der Batterieherstellung wiederum kommt es auf die Luftfeuchtigkeit an. Idealerweise herrschten in solchen Reinräumen „Bedingungen wie in der Sahara.“
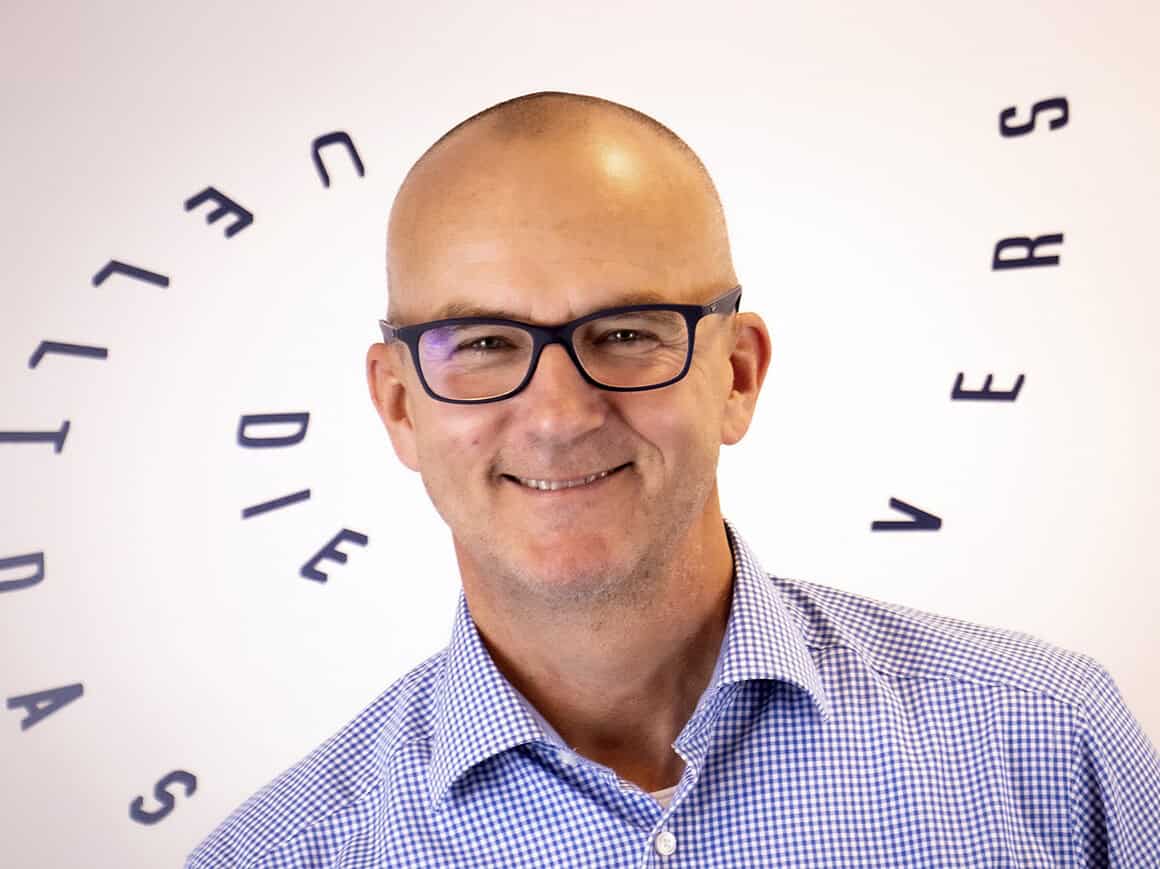
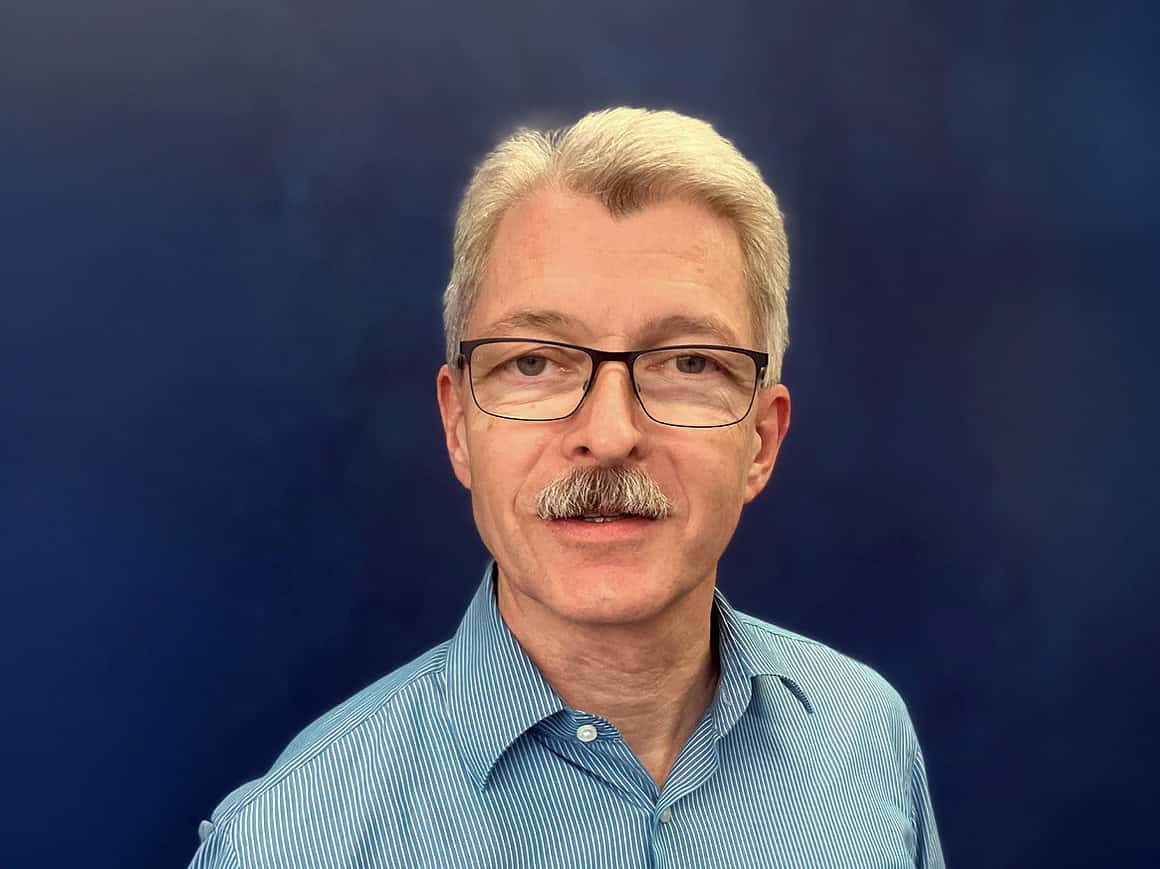
Generell ist ein Reinraum deshalb rein, weil die Luft so gut wie keine Partikel aufweist. Und die gibt es sonst immer: Mikroskopisch winzige Teile wie Feinstaub, die herumschwirren, im Fertigungsprozess von Microchips aber immensen Schaden anrichten können. In einem normalen Büro zum Beispiel befinden sich bis zu einer halben Million Partikel auf einem Kubikmeter Luft. In Reinraumklasse 1 ist nur ein einzelner Partikel erlaubt, der größer als 0,5 Mikrometer ist. Um das einzuordnen: Ein menschliches Haar hat einen Durchmesser von 70 Mikrometer.
Diese strenge Regelung ist nötig, weil das Maß, auf denen die Microchips operieren, ebenfalls winzig ist. „Die minimale Größe der Strukturen in den Hall-Sensoren, die wir bauen, liegt zwischen 450 und 800 Nanometern“, erklärt Dirk Heinen. Ein Nanometer ist ein Milliardstel Meter. Jeder versehentlich mitverbaute Partikel, und ist er noch so winzig, kann Kurzschlüsse verursachen.
Um die Luft reinzuhalten, ist ein kompliziertes Verfahren nötig. In einem Reinraum sind alle Oberflächen perforiert – jeder Tisch, jedes Tablett, jedes Wägelchen, aber auch die Decken und Wände, damit die Luft möglichst ungestört zirkulieren kann. Oberhalb der Decke befinden sich Filter, die die Luft säubern, spezielle Ventilatoren drücken sie durch die Filter nach unten. Mit einer Geschwindigkeit von rund 30 Zentimetern in der Sekunde bewegt sich der kontinuierliche Luftstrom durch den Produktionsbereich. Die Luft nimmt die Partikel mit, führt sie durch den Lochboden in das darunterliegende Stockwerk, wird umgewälzt, und strömt wieder durch den Filter, wird erneut nach unten gedrückt. „Etwa 400-mal pro Stunde wird auf diese Weise das gesamte Luftvolumen ausgetauscht“, erklärt Dirk Heinen.
Testen, testen, testen
Die Produktionsschritte im Reinraum sind komplex und langwierig: Bei TDK-Micronas werden die Strukturen von Masken in einem fotolithografischen Prozess optisch verkleinert und vielfach neben- und untereinander auf die noch blanken Wafer übertragen. Daraus entsteht in mehreren hundert Arbeitsschritten Schicht für Schicht der fertige Microchip. Die Wafer werden am Ende zersägt, damit die einzelnen Chips verbaut werden können. Vom Beginn bis Ende des Produktionsprozesses vergehen Monate.
Die Boxen, in denen sich die empfindlichen Wafer befinden, dürfen ausschließlich einzeln per Hand transportiert werden. Wer mehr bewegen will, muss ein Wägelchen benutzen. Die Anlagen, etwa 150 sind es bei TDK-Micronas, stehen in eigenen Räumen. Ein Wafer wird niemals in diesen Raum gebracht. Dafür bestücken die Operatoren – das sind die Frauen und Männer, die die kostbaren Scheiben transportieren, die Prozesse starten und überwachen – die Anlagen über eine spezielle Ladestation in den Gängen, die die Räume voneinander trennen. Grund: Die großen Maschinen werden regelmäßig gesäubert, gewartet, überprüft. Dabei können Partikel entstehen, die so weit wie möglich von den Wafern ferngehalten werden sollen.
Zu all den Abläufen gesellt sich eine Vielzahl an Tests. Denn da man Fehler mit dem bloßen Auge nicht sehen kann, lässt TDK-Micronas in der laufenden Fertigung ständig überprüfen, ob die Produktionsprozesse tun, was sie tun sollen. „In der Halbleitertechnik ist die Herausforderung, dass die qualitativen Ansprüche so hoch sind, dass man Fehler unbedingt vermeiden muss. Wenn Sie gut sind, kämpfen Sie gegen extrem kleine Fehlerraten“, erläutert Dirk Heinen, der für die Technologie verantwortlich ist. Echte Kundenretouren aufgrund von im Reinraum eingebauten Fehlern kämen so gut wie nie vor.
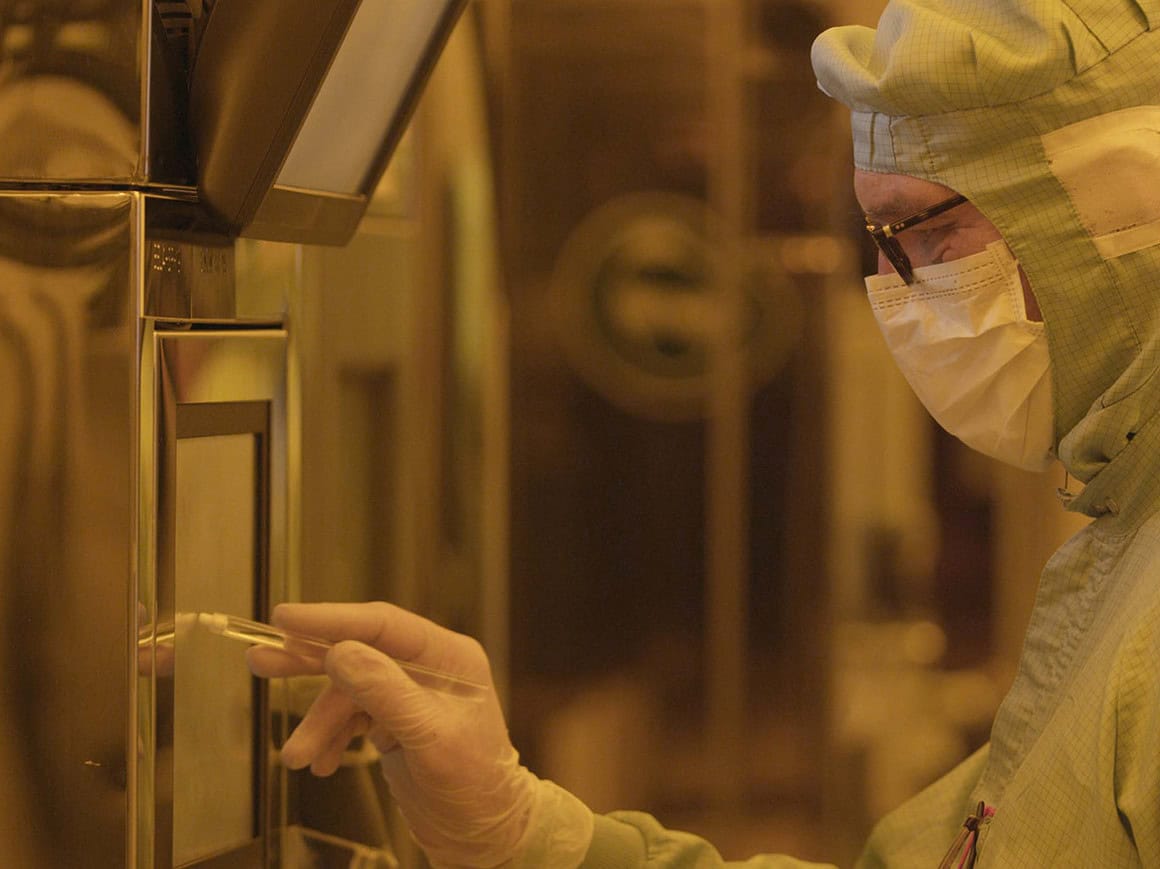
Der Reinraum selbst läuft rund um die Uhr, TDK-Micronas arbeitet im Drei-Schichten-System an sieben Tagen in der Woche. Rund 200 Personen sind im Reinraum beschäftigt: Das sind die Operatoren sowie Maintenance-Mitarbeiter, die die Anlagen warten und pflegen. Dazu kommen Ingenieurinnen und Ingenieure.
Vom Besuchergang sehen wir die Maschinen, die Wafertransportboxen, die Menschen, die einzelne Prozesse starten. Und am Ende des Ganges wartet ein besonderer Bereich: Es ist der Raum, in dem die Strukturen der Fotolithografiemasken auf die Wafer übertragen werden. Dieser Reinraum ist einer mit noch spezifischeren Eigenschaften. Licht und Fenster sind orange, um die optischen Prozesse nicht durch äußere Lichtschwankungen zu beeinflussen, zudem ist die Temperaturkonstanz hier noch wichtiger als im Rest. Im Reinraum herrschen 22 Grad, plus/minus ein Grad Abweichung ist erlaubt. „Im Fotobereich sind die die Toleranzen noch geringer, um die Prozessstabilität zu garantieren“, erklärt Heinen.
Hinzu kommt eine weitere Besonderheit: Das gesamte Gebäude ist schwingungsgeschützt, es steht dafür unter anderem auf einer einen Meter dicken Betonplatte. Der Fotoraum als sensibelster Bereich ist noch mal zusätzlich vom Rest des Gebäudes entkoppelt, eine Gummilippe am Boden umgibt ihn und sorgt dafür, dass keinerlei Schwankungen möglich sind. Wer dachte, es sei in der Halbleitertechnik ja ohnehin alles im klein-klein verloren, hat das noch nicht gehört: „Die Prozesskontrollen der Strukturen, mit denen wir bei den Fotoprozessen arbeiten, liegen in der Größenordnung von Nanometern“, sagt Dirk Heinen. Doch das geht noch genauer: „Bei kritischen Schichtdicken wird sogar von der Größenordnung Angström gesprochen, wobei wir Bruchteile von Angström berücksichtigen.“ Zur Erinnerung: 1 Nanometer ist 1 Milliardstel Meter. Und ein Angström entspricht 0,1 Nanometern. Kein Wunder, dass hier wirklich gar nichts schwanken darf.
Zum Unternehmen
Der Standort Freiburg wurde 1958 gegründet, 2016 von der japanischen TDK Corporation übernommen und umfirmiert in TDK-Micronas GmbH. Mit circa 1000 Mitarbeitenden entstehen hier unter anderem Hall-Sensoren, zum allergrößten Teil für die Automobilindustrie. Sehr vereinfacht erklärt können die Sensoren, benannt nach ihrem Erfinder, dem US-Physiker und Harvard-Professor Edwin Hall, Magnetfelder in einem elektrischen Umfeld messen. „Mit ihnen kann eine Vielzahl von Messgrößen bestimmt werden: Winkel, Rotation oder Drehmoment“, erklärt Dirk Heinen. Im Auto sind es vielfältige Anwendungen, sie dienen zum Beispiel zur Bestimmung der Drehzahl, justieren die Beleuchtung oder warnen, wenn der Sicherheitsgurt nicht angelegt ist. „In modernen Autos gibt es bereits mehr als hundert mögliche Anwendungen für Sensoren“, sagt Unternehmenssprecherin Julia Andris. Es sei ein Grund dafür, dass es der TDK-Micronas im Gegensatz zu vielen anderen schwächelnden Automobilzulieferern derzeit nicht schlecht geht. „Unser Wachstum hängt nicht von der Anzahl hergestellter Autos ab. Wir merken zwar die Effekte der Krise, sind aber weniger davon betroffen. Wir stehen gut da, weil die Nachfrage nach Sensoren insgesamt immer weiter steigt.“ Nach Unternehmensangaben hat TDK-Micronas bislang insgesamt über sechs Milliarden Hall-Sensoren an den Automobil- und Industriemarkt ausgeliefert.