Wie aus einem kleinen Textilzulieferer ein weltweit führender Anbieter für thermoplastische Klebelösungen wurde, hat uns Abifor-Chef Peter Hinder verraten.
Text: Julia Donáth-Kneer • Fotos: Alex Dietrich
Heutzutage bohrt fast niemand mehr die Fliesen im Bad an. Es ist nicht nötig, weil verschiedene Hersteller Lösungen anbieten, die man an die Wand kleben kann und die genauso gut halten: für Klopapierrollenhalter, Handtuchstangen, Duschablagen. Was im Kleinen im Heimwerk funktioniert, hält auch im Großen in der Industrie Einzug. Stichwort: Kleben statt bohren.
„Der Klebemarkt ist ein Wachstumsmarkt“, sagt Peter Hinder. Der gebürtige Schweizer ist CEO der Abifor AG. Das Unternehmen hat seinen Hauptsitz in Zürich und produziert im badischen Wutöschingen, in der Nähe der Schweizer Grenze an den südöstlichen Ausläufern des Schwarzwalds. „Es ist in der Fertigung günstiger und schneller, zwei Komponenten miteinander zu verkleben, statt sie zu verschrauben, zu nieten oder zu vernähen“, erklärt der 53-Jährige. Deshalb sei das Verfahren zum Beispiel in der industriellen Automobilfertigung gefragt.
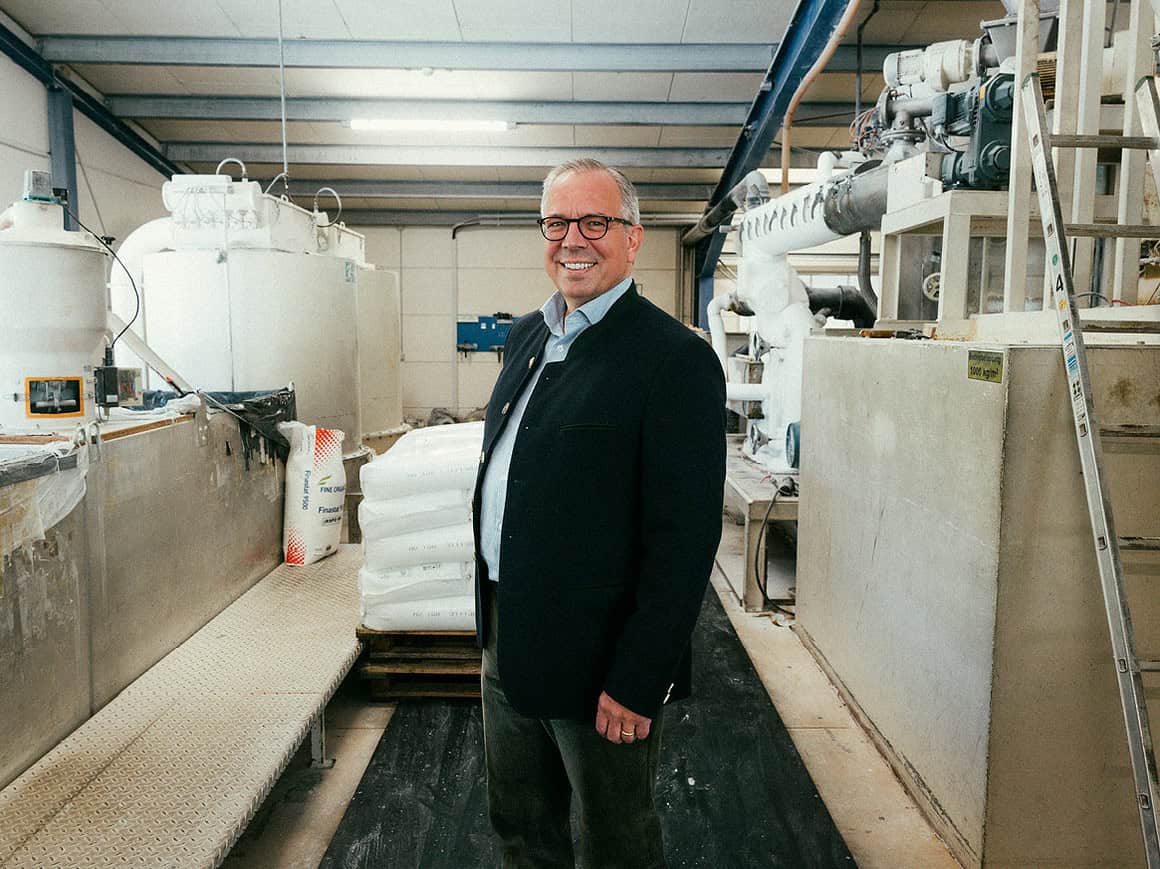
Beim Kleben gehe es nicht unbedingt um einen Preisvorteil des Materials – gute Klebstoffe können sehr teuer sein – sondern um den Zeitgewinn in der Produktion, erklärt der Experte. Zudem kann man Gewicht einsparen, was zum Beispiel bei der Herstellung von E-Autos interessant ist. Außerdem sind Lithium-Ionen-Batteriezellen, wie sie in Elektroautos verwendet werden, keine statischen Objekte wie Schrauben oder Nägel. „Sie verhalten sich bei Benutzung dynamisch und müssen während der Fahrt Vibrationen aushalten“, sagt Hinder. „Daher sind hier Verfahren mit teilelastischen Klebern die bessere Lösung.“
Aktuell landen fast 50 Prozent der Produkte von Abifor in der Automobilindustrie – bei weitem nicht nur in E-Autos. Hutablagen, Innenverkleidung, Bodenteppiche, Lenkräder, die Kofferraumauskleidung werden beispielsweise verklebt. Kunden sind nicht die Automobilhersteller selbst, sondern die Zulieferer.
Die Ursprünge liegen jedoch woanders: in der Textilindustrie. Hemdkrägen und Anzüge werden mit Klebepulver gestärkt, die einzelnen Stoffschichten miteinander verklebt. Dafür setzte das 1957 gegründete Unternehmen von Anfang an auf thermoplastische Lösungen statt auf lösungsmittelbasierte Klebstoffe. Thermoplastisch heißt: Wenn Klebepulver erhitzt wird, schmilzt es und wird wieder fest, wenn es erkaltet. Dieser Vorgang ist reversibel, er kann durch Abkühlung und Wiedererwärmung beliebig oft wiederholt werden.
Aus dem Banking in die Industrie
Dass man mit thermoplastischen Verfahren Stofflagen miteinander verkleben kann, wissen alle, die schon mal einen Flicken auf eine Hose gebügelt haben. Viel mehr als das kannte CEO Peter Hinder auch nicht, als er in die Industrie wechselte. Der gebürtige Schweizer war eigentlich im Finanzwesen tätig, leitete 2016 die großen Umstrukturierungsprogramme der Deutschen Bank in Frankfurt und in Zürich. „Ich bin mein Leben lang gereist, hatte Büros in ganz Europa“, erinnert sich Hinder. „Doch als ich 50 wurde, dachte ich, ich muss noch mal etwas ganz anderes machen.“ Durch Zufall lernte er Rolf Wickihalter kennen, den damaligen Inhaber von Abifor, der die Firma mit Investoren übernommen und lange geführt hatte. Wickihalter suchte eine Nachfolgelösung. Hinder stieg ein, übernahm 80 Prozent der Anteile und leitet jetzt gemeinsam mit Markus Kohlhof das Unternehmen, das heute insgesamt rund 50 Menschen beschäftigt, mehr als die Hälfte davon in Wutöschingen.
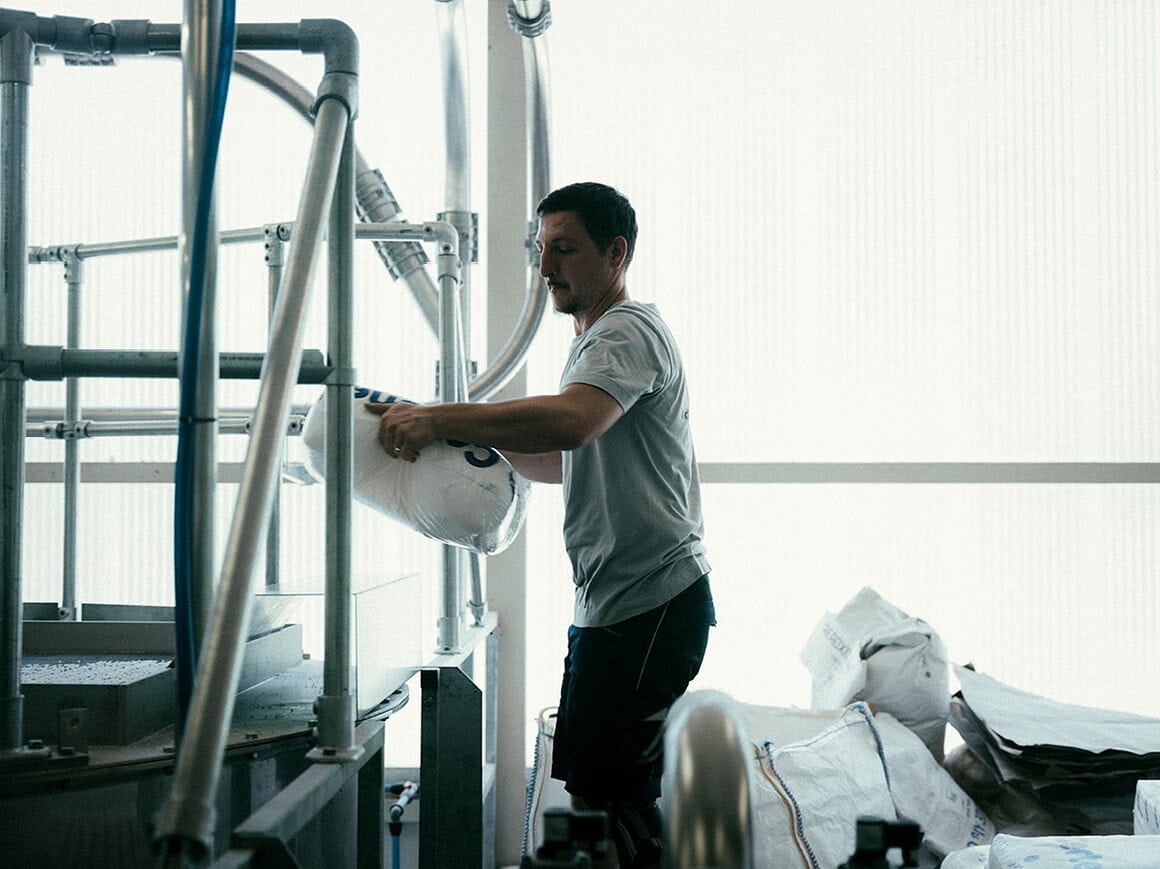
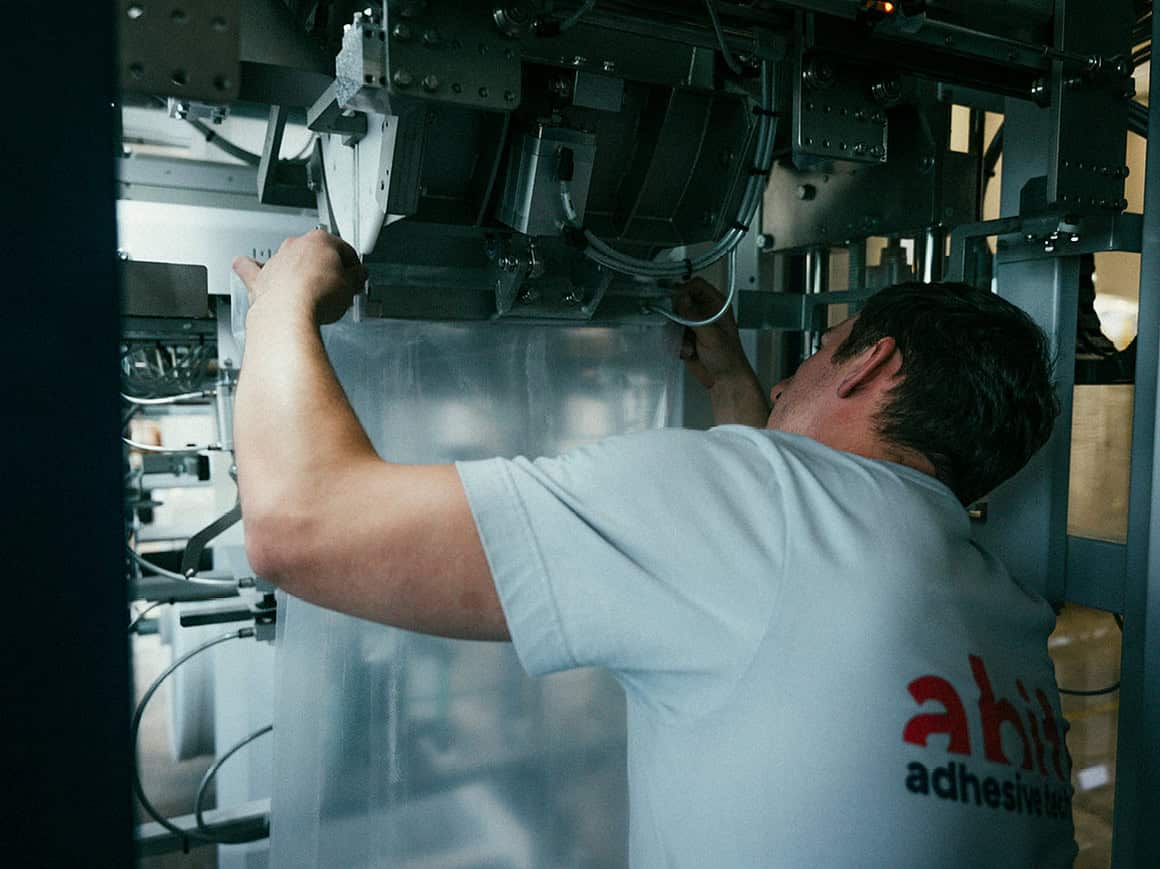
Dort war Ende der Neunzigerjahre das Hauptgeschäft weggebrochen, als die Textilindustrie größtenteils nach Asien abwanderte. In der Folge musste sich Abifor in Europa diversifizierter aufstellen. Zur Textil- kamen die Auto-, Leder- und Bauindustrie. 2005 gründete das Unternehmen eine Niederlassung in Shanghai. Die Produkte kommen zum Beispiel in Matratzen, Handtaschen, Schuhen oder Folien für den Bau vor.
Abifor hat eigene Labore, ist aber keine Chemiefabrik. Das Unternehmen produziert die Rohmaterialien nicht selbst, sondern kauft sie als Granulate von großen Herstellern ein. „Wir sind weltweit die einzigen, die sämtliche Kunststoffe abdecken, die sich für thermoplastisches Kleben eignen und diese nicht nur als Pulver, sondern auch als Webs, Filme und Netze anbieten“, sagt Peter Hinder.
Es geht immer darum, zwei verschiedene Materialien miteinander zu verkleben. „Wir sprechen in der ersten Phase mit den Entwicklern und suchen gemeinsam die richtige Lösung“, erklärt Hinder, der in seinen ersten Monaten beim Unternehmen in der Produktion aushalf, um die Verfahren kennenzulernen. Denn die können mitunter komplex sein: Jedes Entwicklungsteam hat spezifische Anforderungen, jede Branche arbeitet mit unterschiedlichen Materialien. Der eine Kunde braucht Flammschutz, der andere will poröses Material verkleben, der dritte muss biologisch abbaubare Lösungen umsetzen. „Es gibt Standards, aber vieles entsteht in Zusammenarbeit mit der Forschungs- und Entwicklungsabteilung des jeweiligen Kunden“, erklärt der Geschäftsführer.
Stichwort Nachhaltigkeit
Auch die Anforderungen an den Klebemarkt ändern sich, an Nachhaltigkeit kommt niemand vorbei. Wobei die Thermoplastik als Zugpferd gilt, da sie ohne Lösemittel arbeitet. „Die Nachfrage nach biobasierten Klebstoffen sowie nach neuen Kunststoffen, die auch recycelbar sind, steigt“, sagt Hinder. Darauf muss auch Abifor reagieren. Ein Trend sei Monomaterial, das heißt, dass Bauteile, die früher aus verschiedenen Stoffen zusammengesetzt wurden, nun aus ein- und demselben Grundprodukt bestehen sollen, damit sie am Ende besser recycelt werden können. Wie man sie produziert und miteinander verklebt, damit sie trotz neuer Zusammensetzung die gleichen Eigenschaften behalten, daran arbeitet man in Wutöschingen.
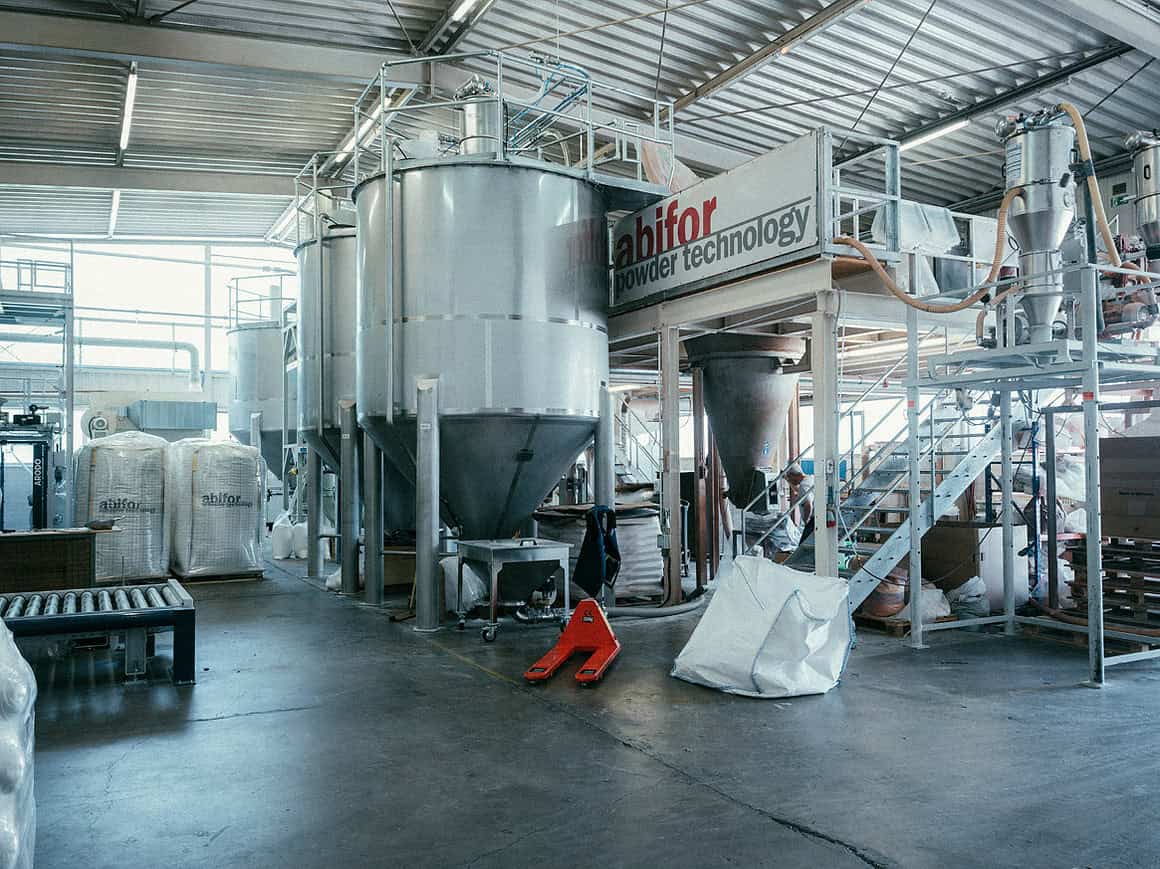
Abifor ist breit aufgestellt, wächst jährlich zweistellig. Dennoch merkt das Unternehmen die Konjunkturschwankungen der Branchen. Im Automotivesektor sei es gut, dass man nicht von ein oder zwei Großkunden abhängig sei, meint Hinder. Vor allem in der Baubranche gab es zuletzt eine größere Delle. „Früher hat sie mal 20 Prozent des Gesamtumsatzes ausgemacht, das ist deutlich zurückgegangen auf etwa 10 Prozent. Dafür wachsen andere Bereiche.“ Das Unternehmen selbst will auch wachsen. Derzeit plant Abifor in Wutöschingen einen Neubau, der mit 7000 Quadratmetern etwa doppelt so groß sein wird wie der aktuelle. Der Umzug ist für 2026 angesetzt.